SCREENING
Rotary screen
The circular screen is designed to separate the fines generated during the pelletizing process and recirculate them to the pelletizer.
Circular screens allow a precise classification of the material into different particle size fractions, adapting to the specific requirements of the process.
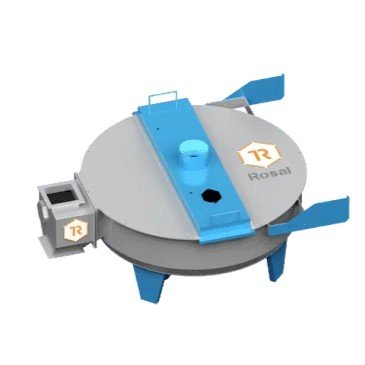
Features
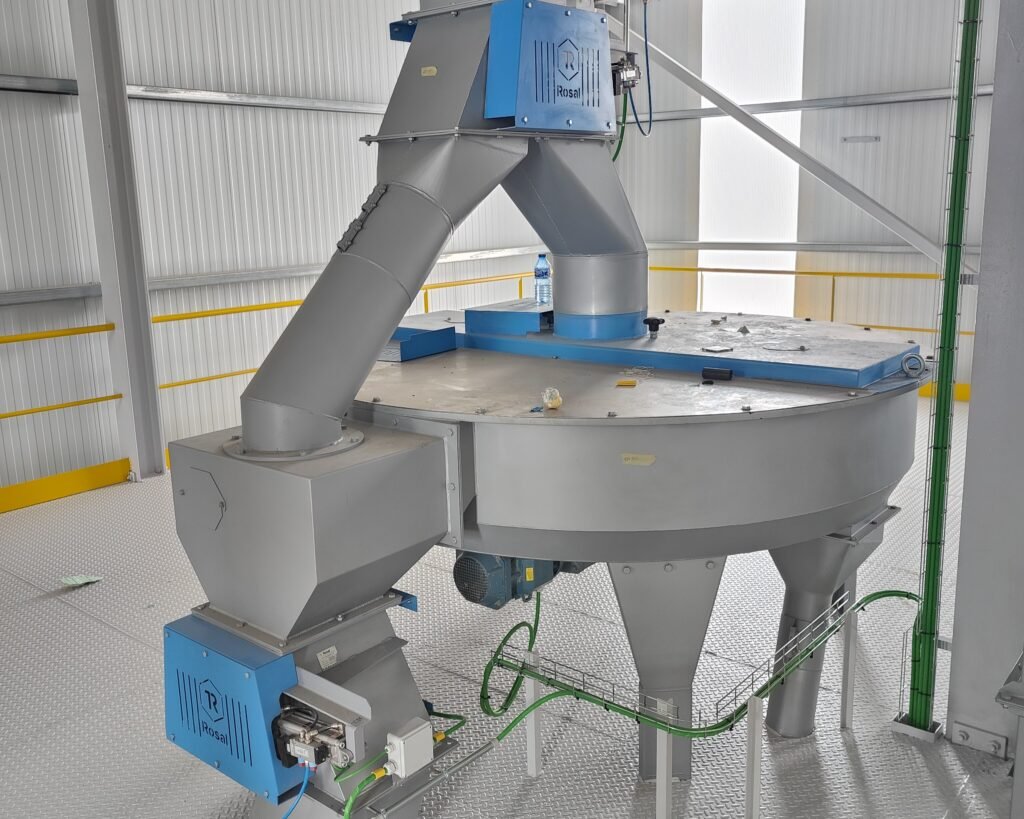
Sieving
Great versatility
The machine is designed with a horizontal rotating screen driven by a geared motor. Manufactured in carbon or stainless steel, it adapts to various industrial needs thanks to its wide range of diameters, ideal for all types of production.
Design
Compact and efficient screen
The Rosal circular screen operates without vibration and with a minimum noise level. Its compact design and low energy consumption optimize space and resources.
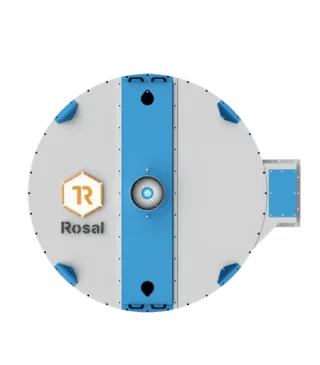
Models
Model | Motor power (kW) | Grill diameter (mm) | Maximum capacity (Tn/h) |
---|---|---|---|
CH-531 | 5,5 | 12 | 25 - 30 |
CH-541 | 7,5 | 12 | 50 - 60 |
CH-551 | 15 | 14 | 100 |
CH-561 | 18,5 | 14 | 150 |
CH-571 | 18,5 | 14 | 200 |
Frequently Asked Questions
They can be installed at the flour inlet to eliminate by-products and minerals, or after the mixer, before the pelletizer, in order to protect the latter from any foreign body that could be incorporated into the flour during the process.
Our flour sifters are specially designed to meet the needs of the agro-industrial sector:
Compound feed mills
Cereal processing plants
Flour mills
Pet food factories
Biomass plants
Extrusion plants
Oilseed handling
Handling of cereals, flours and their by-products in general
Staggered maintenance is recommended:
Weekly: dust cleaning and visual control.
Monthly: revision of sieves, brushes and electrical connections.
Annual: thorough cleaning of the interior and greasing of shafts.
Every 10 years: disassembly of the motor, replacement of bearings and seals.
It is certified for areas classified as ATEX Zone 22 (explosive dust environments), complying with Directive 2014/34 EU, which guarantees its safe use in environments with risk of explosion.
They should not be used with products that do not flow easily or that have a high dust explosive index, as these could create unsafe conditions during screening.
It has 2 outlets, one for clean product and one for impurities or unwanted materials, facilitating efficient in-line separation.
Request more information
Leave us your data and questions and a circular screen technician will advise you without obligation. Let's talk!
Related machinery
Grain cleaner
Pre-cleaners are designed to protect manufacturing equipment from wood chips, stones and other particles.
Flour sifter
The sifter filters and separates foreign agents such as iron, stones or cardboard from the flours.