MIXING
Ribbon and paddle mixers
The Rosal mixers are designed to be durable and require minimal maintenance.
They facilitate effective homogenization with various products in the animal feed and chemical industry, achieving high production efficiency in reduced mixing times.
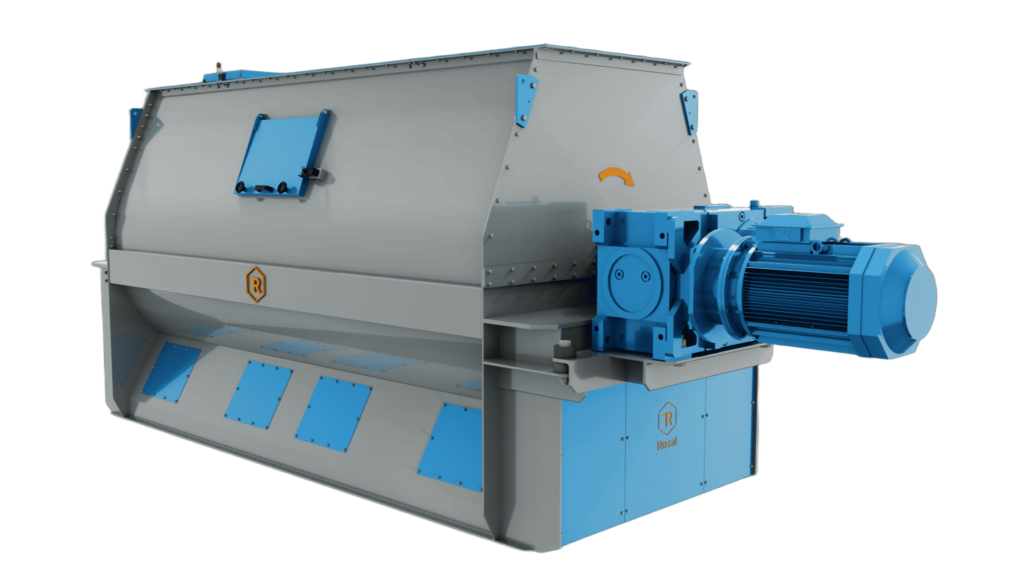
Features
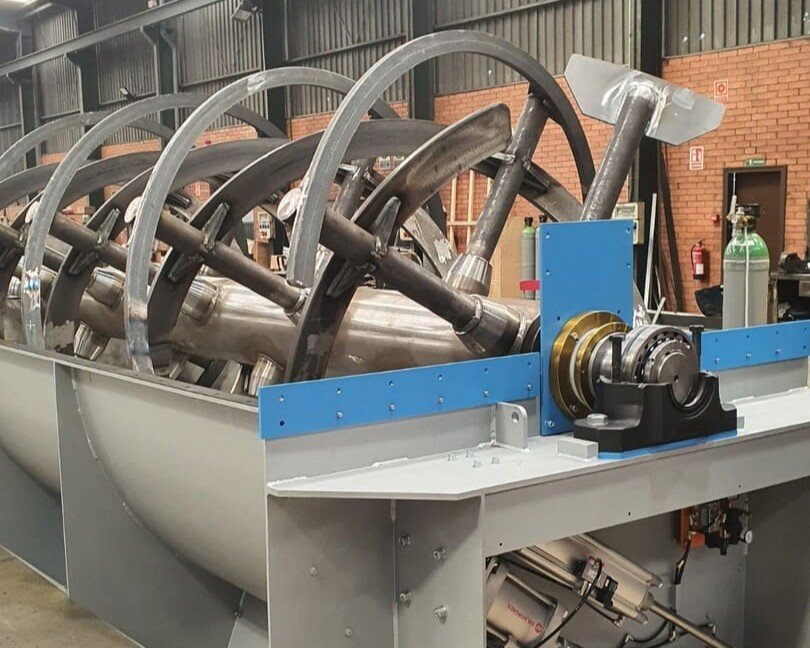
Ribbon
Ribbon mixer
Paddles
Single shaft paddle mixer
Rosal has a wide range of single shaft paddle mixers, from 50 up to 16,000 liters.
Unlike the ribbon mixer, the body of the paddle mixer is cylindrical, adapting to the path of the rotor along the entire vertical axis.
The signle shaft paddle mixer is designed with a bolted, adjustable and interchangeable paddle rotor, which allows for great versatility and adaptability in the mixing process.
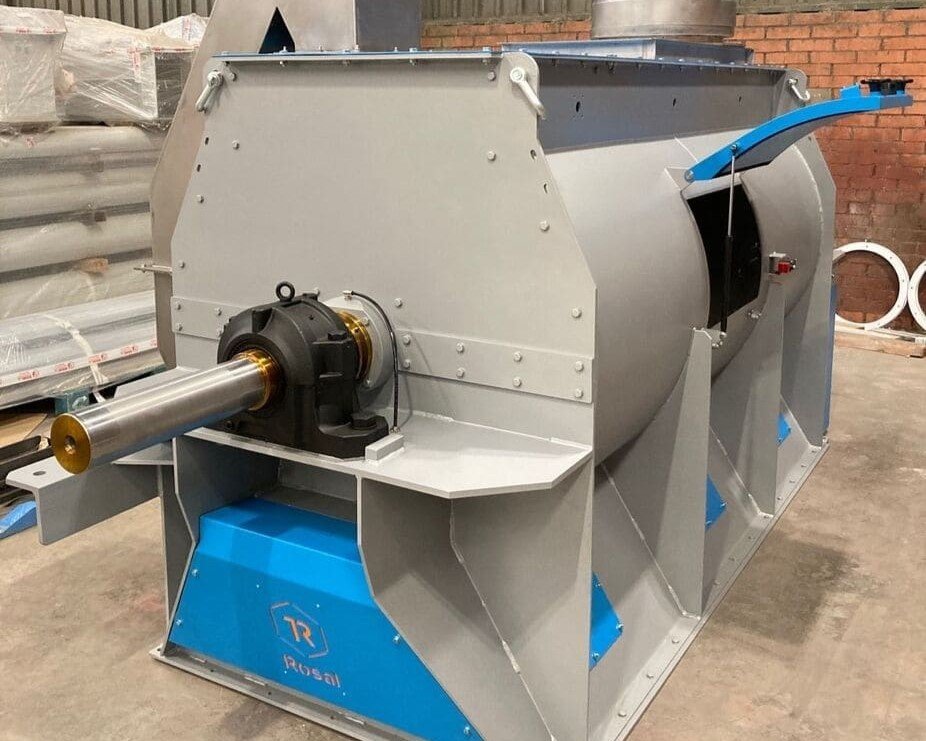
Models
Thinking of all possible mixing fields, Rosal has created different constructive lines of mixers for animal feed.
MHR Mixers
- Ribbon or propeller mixers.
Model | Nominal capacity (liters) | Tank diameter (mm) | Tank length (mm) | Motor power (Hp) |
---|---|---|---|---|
MHR-1000 | 1000 | 800 | 1800 | 5,5 |
MHR-2000 | 2000 | 1000 | 2500 | 10 |
MHR-3000 | 3000 | 1160 | 2700 | 15 |
MHR-4000 | 4000 | 1300 | 3000 | 25 |
MHR-5000 | 5000 | 1360 | 3500 | 30 |
MHR-6000 | 6000 | 1400 | 3800 | 40 |
MHR-8000 | 8000 | 1550 | 4250 | 60 |
MHR-10000 | 10000 | 1700 | 4750 | 75 |
MHR-12000 | 12000 | 1800 | 5100 | 100 |
MHR-16000 | 16000 | 1950 | 5500 | 150 |
MHR-20000 | 20000 | 2100 | 5900 | 180 |
MHR-24000 | 24000 | 2250 | 6300 | 220 |
MPR Mixers
- Paddle mixers.
Model | Nominal capacity (liters) | Tank diameter (mm) | Tank length (mm) | Motor power (Hp) |
---|---|---|---|---|
MPR-1000 | 1000 | 910 | 1900 | 7,5 |
MPR-2000 | 2000 | 1150 | 2400 | 15 |
MPR-3000 | 3000 | 1300 | 2800 | 20 |
MPR-4000 | 4000 | 1450 | 3000 | 30 |
MPR-5000 | 5000 | 1550 | 3300 | 40 |
MPR-6000 | 6000 | 1660 | 3500 | 50 |
MPR-8000 | 8000 | 1820 | 3850 | 60 |
MPR-10000 | 10000 | 1950 | 4200 | 75 |
MPR-12000 | 12000 | 2050 | 4400 | 100 |
MPR-16000 | 16000 | 2300 | 4800 | 125 |
Frequently Asked Questions
The mixer loads ingredients from the top, agitates them with an internal rotor (paddles or belts) and discharges them through a bottom gate after 3-5 minutes of mixing.
The Rosal ribbon and paddle mixers for animal feed achieve a coefficient of variation (CV) lower than 5%, which guarantees a homogeneous and constant mix, even in large volume batches.
The standard mixing time is approximately 4 minutes, although it may vary depending on the formula and ingredients used.
The tanks are manufactured in AISI 316 stainless steel or carbon steel, with thicknesses ranging from 4 to 10 mm depending on the capacity of the equipment. The rotors are made of treated carbon steel for greater durability.
Yes, the industrial mixers are prepared for the addition of vaporized liquids by means of integrated spraying systems, which makes it possible to enrich the mixture with oils, molasses or other additives.
Discharge is by means of a pneumatically operated, fully opening swing gate. It includes pneumatic cylinders, magnetic detectors and vibrator to ensure complete emptying.
They have stop sensors in inspection doors, motor consumption control, hermetic seal and protection against overheating in bearings by means of temperature probes.
Rosal ribbon and paddle mixers have direct drive to the drive shaft by means of hollow shaft reducers with shrink ring. This configuration minimizes possible mechanical losses, reduces maintenance and improves the energy efficiency of the system.
Yes, our industrial mixers allow for speed and mixing time adjustments, among others, which makes it easier to work with different formulas, densities and types of ingredients.
Add macroingredients
Add micro-ingredients
Dry blending
Add fat
Add liquids
Wet mix
- Weekly: dusting and visual inspection.
- Every 4 months: check oil levels and operation of safety devices.
- Every 6 months: greasing of bearings.
- Every 10 years: complete replacement of bearings and overhaul of gearboxes.
Request more information
Leave us your data and questions and a technician in ribbon blenders and industrial blades will advise you without obligation. Let's talk!
Related machinery
Twin shaft paddle mixer
The twin rotor mixer is ideal for mixing products with very different textures, such as pellets, flours and extrudates.
Turbulence mixer
The vertical mixer achieves optimum homogenization levels without deteriorating the product.