GRINDING
Hammer mill
Grinding is one of the most important processes in feed production. The objective is to achieve the optimum particle size by milling the raw materials (wheat, corn, barley, etc.).
The new MMR hammer mill model has been a revolution in the sector due to the productivity guarantees it offers, as well as the new side-opening system that facilitates changing grids and hammers.
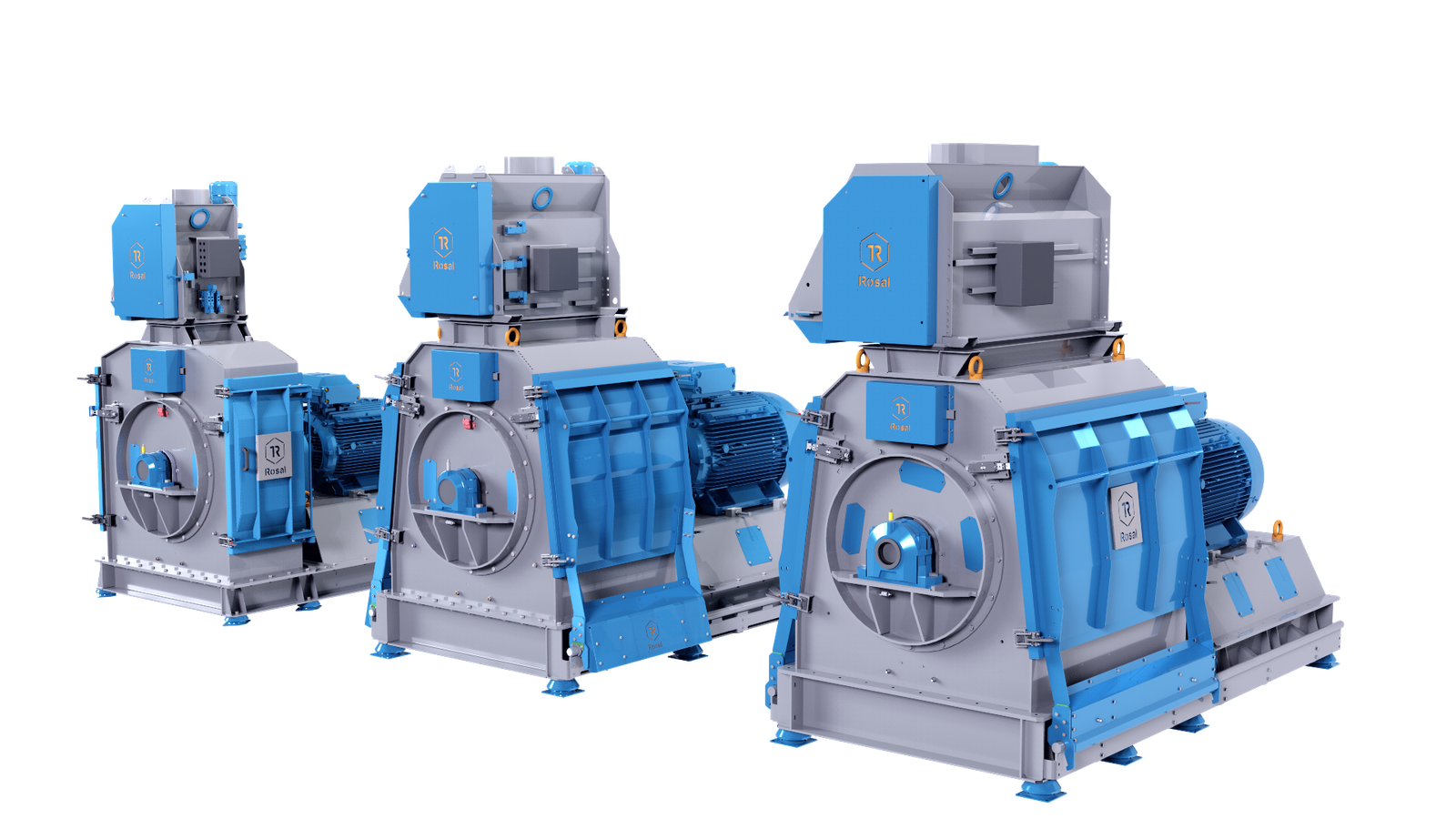
Features
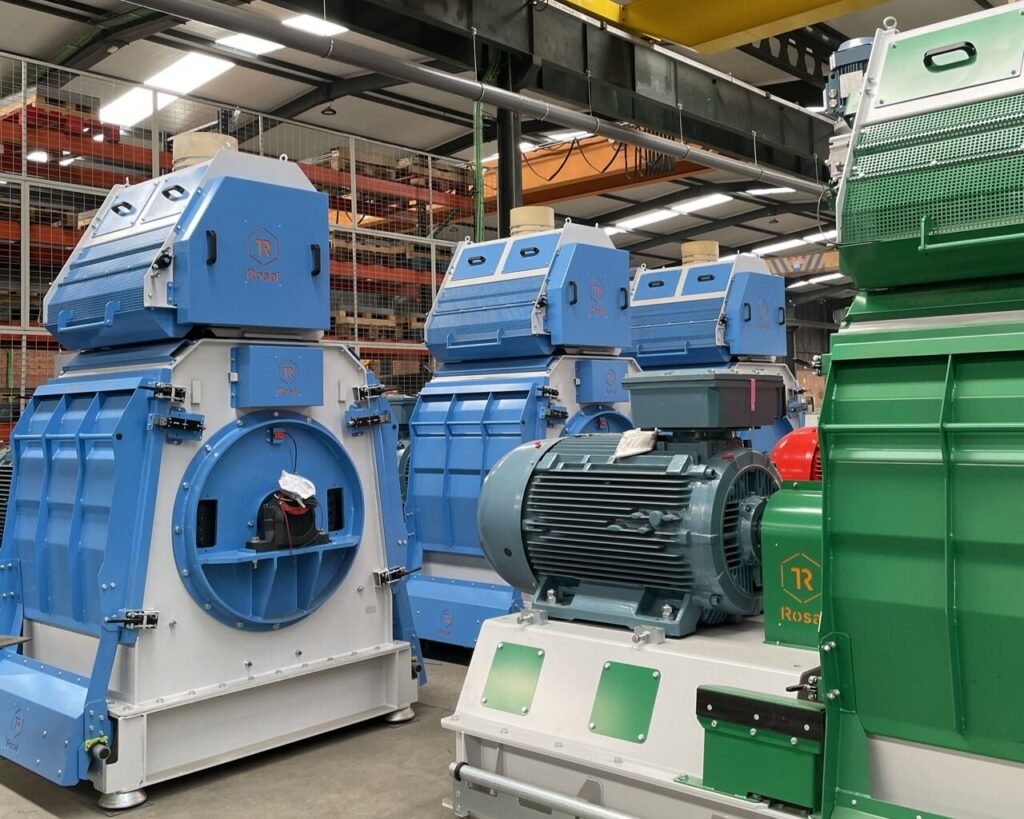
Performance
High-efficiency industrial hammer mills
Our hammer mills are designed to provide high-quality grinding. They are equipped with a rotor fitted with hammers that rotate at high speeds, impacting the product to be ground. This ensures efficient grinding tailored to the final product: livestock feed, pet food, or fish feed.
The hammer mill consists of a steel monobloc body with reinforced construction, supported on a base with special anti-vibration dampers for floor mounting.
Design
Simplified maintenance for optimum performance
The Rosal hammer mills are equipped with two-section circular screens that are easily interchangeable from the outside.
The rotor, which can rotate reversibly clockwise or counterclockwise, ensures maximum utilization of the hammers and sieves.
In addition, easy-access side doors allow for simple and quick maintenance when changing hammers, optimizing operational efficiency.
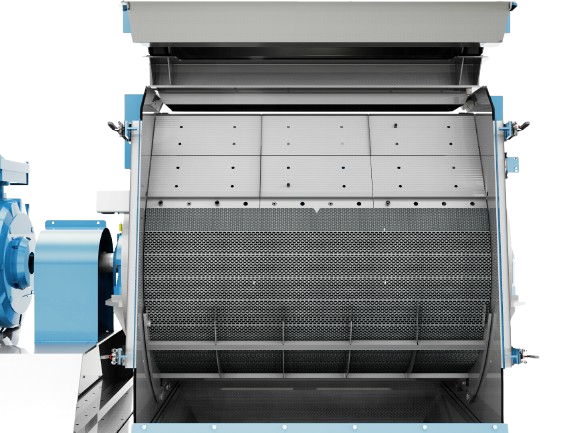
Models
Considering all possible grinding applications, Rosal has created different construction lines. For each hammer mill series, there is the option to install larger motors.
MMR models
- Hammer mills with sliding door and grate holder integrated in the grinding chamber.
- The motor operates at a speed between 1500 and revolutions per minute (rpm).
Model | Motor power (kW) | Number of hammers | Total grill area (m2) | Weight without motor (kg) |
---|---|---|---|---|
MMR-05x10 | 55 - 110 | 48 - 96 | 1 | 2900 |
MMR-10x20 | 110 - 250 | 102 -204 | 2 | 4540 |
MMR-15x30 | 250 - 450 | 156 - 312 | 3 | 5475 |
MRA models
- Hammer mills with removable grinding chamber grate holder.
- The motor operates at a speed of 1500 revolutions per minute (rpm).
Model | Motor power (kW) | Number of hammers | Total grill area (m2) | Weight without motor (kg) |
---|---|---|---|---|
MRA-150 | 110 - 132 | 108 - 152 | 1,3 | 1700 |
MRA-220 | 160 - 250 | 168 - 240 | 2 | 2700 |
MRA-340 | 250 - 355 | 224 | 2,5 | 3100 |
VRE models
- Hammer mills with removable grinding chamber grate holder.
- The motor operates at a speed of 3000 revolutions per minute (rpm).
Model | Motor power (kW) | Number of hammers | Total grill area (m2) | Weight without motor (kg) |
---|---|---|---|---|
VRE-75 | 55 - 75 | 72 - 100 | 0,6 | 1050 |
VRE-150 | 90 - 132 | 108 - 152 | 1 | 1330 |
VRE-220 | 132 - 200 | 168 - 240 | 1,5 | 2300 |
Components of a hammer mill
Separating screen: Separates oversize particles prior to grinding.
Automatic feed regulator: Controls product inflow to maintain a constant load and prevent clogging.
3. Roller feeder: It conveys the material in a dosed form to the crushing chamber.
4. Feed motor reducer: Drives the feeder roller with adjustable speed to suit the type of product.
5. Super strong magnet: Removes metals from the product to protect the mill from damage.
6. Hammer mill
7. Decompression chamber: Reduces internal pressure and facilitates the extraction of the ground product.
8. Extractor thread: It conveys the ground material to the next stage of the manufacturing process.
9. Sleeve filter: Retains air dust generated during grinding.
10. Cuadro eléctrico de regulación de aire
11. Compresor del filtro: Automatically cleans filter bags with compressed air to maintain efficiency.
12. Regulación de caudal
13. Aspirador centrífugo: It generates the necessary air flow to move the product and eliminate particles in suspension.
14. Silencer: Reduces the noise of the suction system.
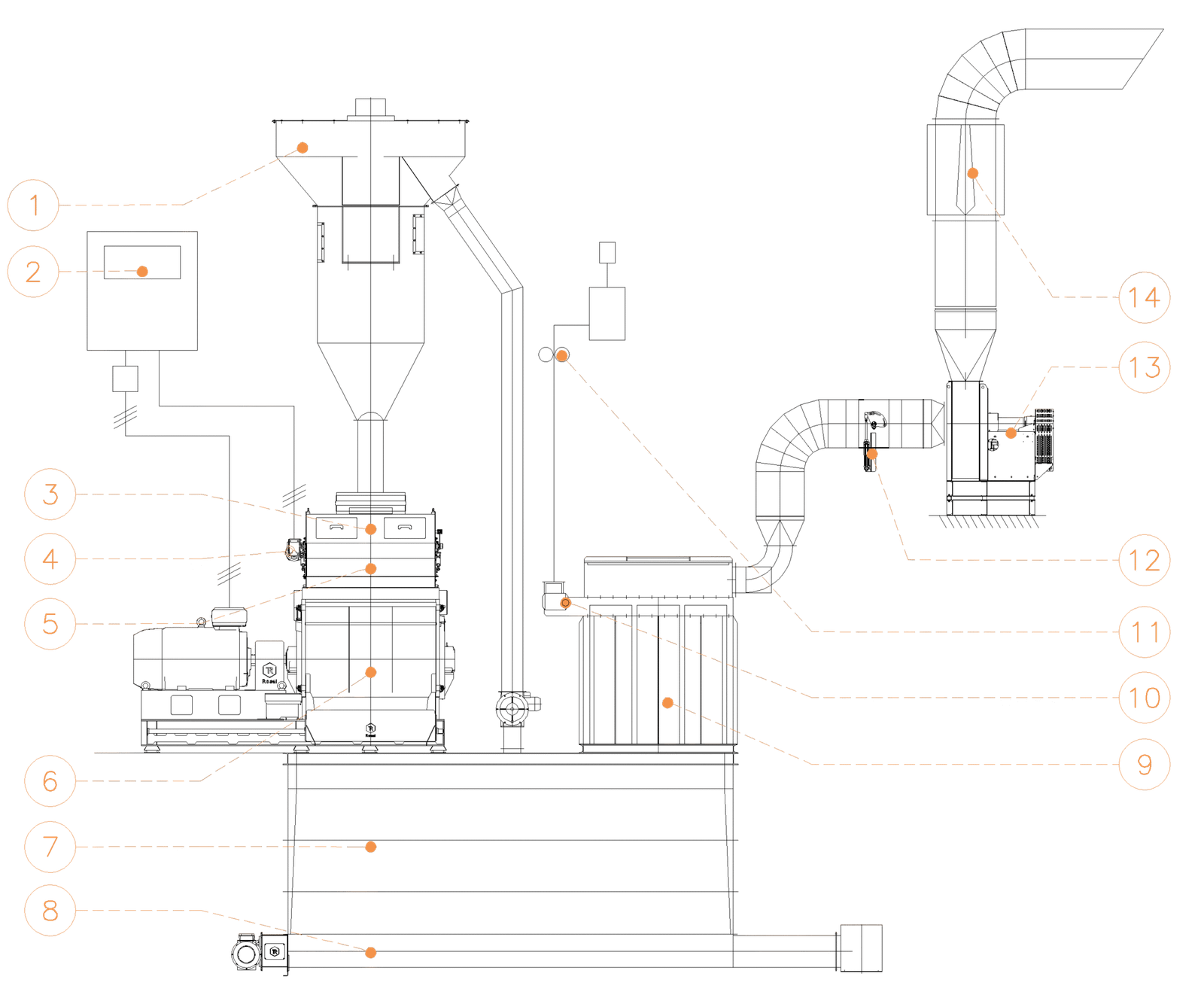
Frequently Asked Questions
The product to be ground enters through the upper mouth and is dosed into a grinding chamber, where it is crushed by mechanical impact from the hammers. The ground product then passes through a sieve and exits through the lower mouth.
The Rosal hammer mills can process:
Agricultural raw materials (corn, wheat, barley).
Flours and by-products.
Biomass (wood chips, husks, straw).
Non-abrasive granular products.
Not suitable for products that do not flow well, with high humidity or with risk of explosion above the permitted Kst limit.
The main factors that determine milling capacity include:
Type and hardness of the material to be processed.
Size of the screen used.
Number and type of hammers.
Motor power.
Rotor speed.
Feeder configuration and feed control.
The screen size determines the particle size of the final product:
Smaller diameter screens generate finer grind but reduce throughput.
Large screens increase capacity, but the product is larger.
The balance between particle size and performance depends on the specific application.
The suction system not only controls dust, but also:
Facilitates the exit of the ground product.
Reduces heat build-up.
Improves the energy efficiency of the process.
Poor design can lead to backflow, clogging or loss of performance due to pressure drops.
The frequency converter allows:
Adjust the motor speed according to the load.
Optimize energy consumption.
Adapt production to different materials.
Reduce mechanical wear and vibration levels.
The reversing system allows changing the direction of rotation of the rotor. This helps to:
Increase the service life of hammers and grills.
Improve wear distribution.
Maintain uniform mill performance.
The hammers are arranged on multiple hammer shafts. The configuration depends on the mill design and the type of grinding required. The hammers must be balanced to prevent excessive vibrations.
The hammers must be replaced if they are worn on both sides or show imbalances. Replacement should be done with the motor completely disconnected, maintaining the original distribution and weight balance to avoid vibrations.
The use of hammers with non-uniform weights generates dynamic unbalance in the rotor, which can cause:
Severe vibrations.
Bearing damage.
Structural fatigue.
Emergency shutdowns due to sensor triggers.
It is mandatory to weigh hammers individually and to use only balanced sets.
The maintenance of a hammer mill includes periodic tasks such as:
Cleaning of accumulated dust (minimum weekly).
Checking the condition of hammers, grills and bearings.
Temperature control in grinding chamber and supports.
Vibration verification by means of accelerometers.
Adequate lubrication according to operating hours.
Scheduled replacement of critical components such as bearings, couplings and hammers.
It depends on factors such as material type, maintenance and workload, but in general:
Hammers: 300 to 1000 hours (depending on product hardness).
Grills: 500 to 2000 hours.
Bearings: up to 10,000 hours with proper maintenance.
Couplings: every 10 years or sooner if they show wear.
Temperature sensors (chamber, bearings).
Accelerometers for vibrations.
Product flow sensors.
PID control of the feeder.
Frequency inverters.
Remote connection for diagnostics via industrial router.
Request more information
Leave us your contact details and questions, and a hammer mill technician will advise you without obligation. Let’s talk!
Related machinery
Roller mill
The roller mill produces a homogeneous grinding, with a minimum percentage of fines.
Flaking mill
The flaking mill produces cereal flakes, ideal for livestock due to their optimal digestibility.